Fiberglass Cable Tray
For more than 30 years, MP Husky's Fiberglass Cable Tray systems have been tested and proven in the harsh environment of the offshore Oil & Gas industry. Our Fiberglass Cable Tray gives you the load capacity of steel, plus the inherent characteristics afforded by Pultrusion Technology: non-conductive, non-magnetic, and corrosion-resistant. These characteristics reduce shock hazard and make our FRP cable tray transparent to radio waves, radar and microwaves.
Although light in weight, the strength to weight ratio surpasses that of equivalent steel products. Our Fiberglass tray weighs 1/3 that of steel trays and is pound for pound stronger. This makes the tray easy to install, reduces the possibility of lifting accidents, and lowers transportation costs. MP Husky Fiberglass Cable Tray is available in both polyester and vinylester resin systems. They are manufactured to meet ASTM E-84, Class 1 Flame Rating and self-extinguishing requirements of ASTM D-635. It will not rust, nor does it ever require painting. FRP cable tray is available in two colors: gray (polyester resin) and beige (vinylester resin), with custom colors available upon request. A surface veil is applied during the pultrusion process to ensure a resin-rich surface for superior corrosion resistance, as well as an ultraviolet exposure barrier.
From paper mills to refineries to laboratories, sound electrical design requires an adaptable FRP cable support system that is reliable. Above all, durability and resistance to corrosion lead to lower overall costs during the life of the installation, so contact us today to find out if our Fiberglass system is right for your application.
- FRP Cable Tray
- Corrosion Resistance
- Strength and Durability
- Fire Retardant
- Bonded Construction
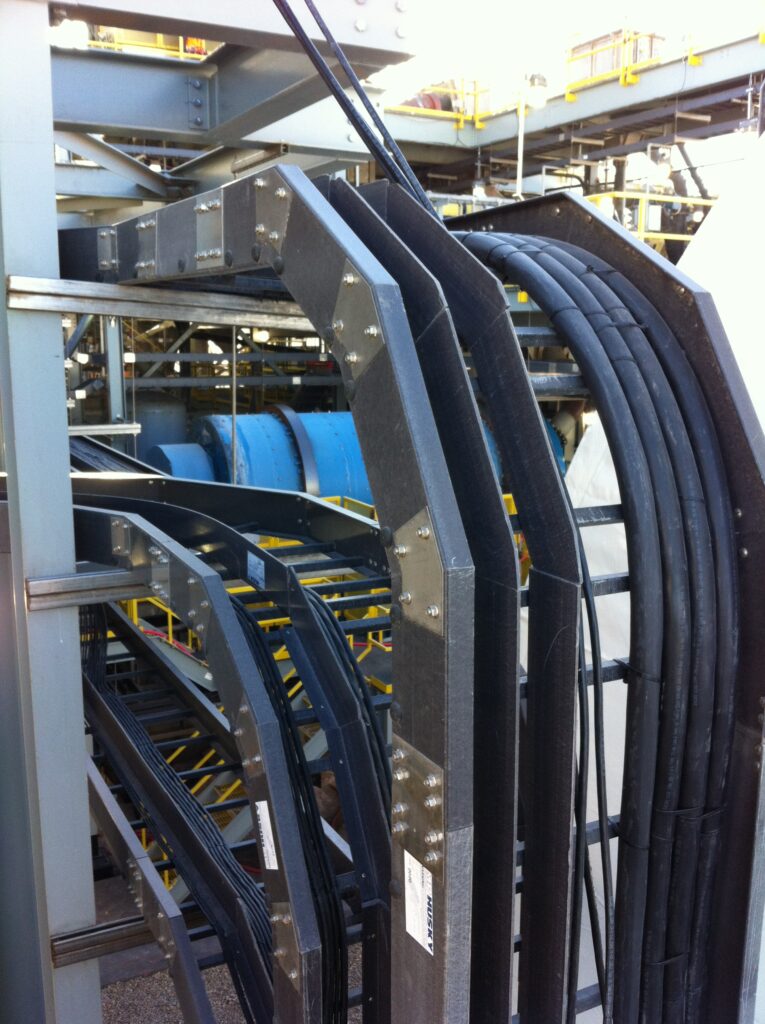
Fiberglass Cable Tray Technical Data
Properties of MP Husky Fiberglass Cable Tray
The data in this section presents the minimum ultimate values from testing in conformance to ASTM procedures. These values are obtained from coupons machined from MP Husky fiberglass shapes and function as a proof test for the MPHusky composite. MP Husky Corporation verifies the full section bending Modulus of Elasticity using a simple beam concept at the start of each production run and periodically thereafter. The designer must consider environmental factors in designing for the actual application. These factors include elevated temperature and corrosive materials.
Fiberglass Cable Tray Temperature Effects
The approximate retention of mechanical properties at elevated temperatures are:
Temperature | Polyester | Vinyl Ester | |
FRP Ultimate Stress | 100°F | 85% | 90% |
125°F | 70% | 80% | |
150°F | 50% | 80% | |
185°F | not recommended | 75% | |
200°F | not recommended | 50% | |
FRP Modulus of Elasticity | 100°F | 100% | 100% |
125°F | 90% | 95% | |
150°F | 85% | 90% | |
185°F | not recommended | 88% | |
200°F | not recommended | 85% |
These recommendations are based on the normal MP Husky proprietary resin system. MPHusky Corporation can process other resin systems to achieve higher temperature ratings for specific applications.
Fiberglass Cable Tray Corrosion Effects
As a general rule, the isophthalic polyester resin is resistant to most acidic attacks while the vinyl ester resin is resistant to acids and bases. The effect of corrosive chemicals is temperature dependent with elevated temperature increasing the corrosion activity. MP Husky Fiberglass cable tray incorporates a synthetic veil on the surface of all structural shapes which causes a resin rich layer which enhances corrosion protection.
Fiberglass Cable Tray UV (Ultraviolet Radiation) Effects
UV is a sunlight produced environmental attack of FRP composites. The synthetic surfacing veil also aids in protecting the composite from UV degradation, the effect of which is sometimes referred to as "fiber blooming". MPHusky polyester and vinyl ester also contain a UV inhibitor to enhance the protection against sunlight.
There is a large variation in the degree of fading from UV degradation based on the color selected. While this fading is undesirable, the structural integrity of the composite will remain unaffected as a surfacing veil is utilized. Coating with materials such as UV stabilized polyurethane based paints are very effective in maintaining the color and offer the optimum long-term protection from UV attack.